Robotic Pick & Place + Assembly
Product image
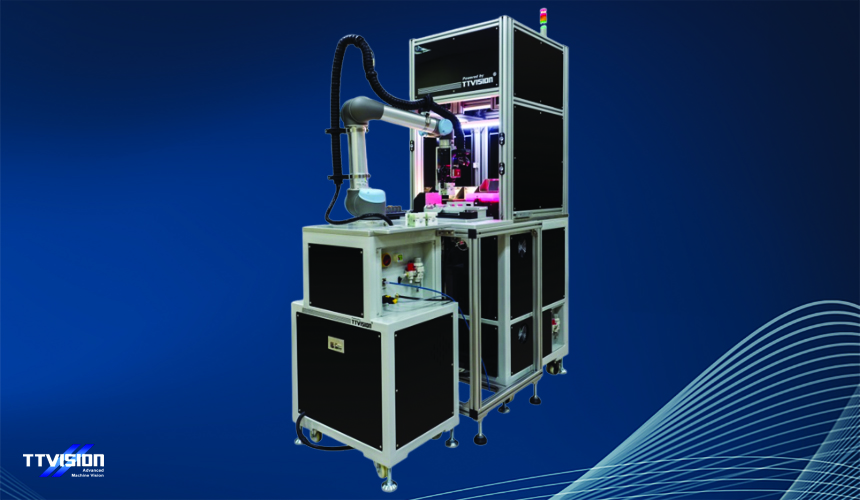
Robotic Pick & Place + Assembly
Description
The Robotic Pick & Place + Assembly system offers a sophisticated solution for automating assembly tasks with precision and efficiency. With vision-guided technology, collaborative robotics, and customizable end-effectors, this system is designed to adapt to a variety of assembly challenges.
Features
- Vision-Guided High Accuracy Pick and Place:
Implement advanced vision guidance for high-accuracy pick-and-place operations. The robotic system utilizes vision technology to precisely identify and handle objects, ensuring optimal placement accuracy in assembly processes. - Automated Part Assembly with UR5 Cobot:
Achieve seamless part assembly using the UR5 collaborative robot (cobot). The collaborative nature of the UR5 ensures safe interaction with human operators and allows for efficient automation of assembly tasks. - Customized End-Effector with Vacuum Pickup:
Tailor the robotic system to your specific assembly needs with a customized end-effector featuring vacuum pickup capabilities. This design ensures versatility in handling a variety of components during the pick-and-place and assembly processes. - Modular System with Docking Capability, Made Possible with Vision Calibration:
Embrace modularity in your assembly processes with a system that supports docking capabilities. Vision calibration ensures precise alignment and compatibility between different modules, enabling a flexible and scalable assembly system. - High-Performance Flexible Component Feeder System with Overhead Camera:
Integrate a high-performance flexible component feeder system featuring an overhead camera to singulate bulk parts. This system optimizes part presentation, ensuring a smooth workflow in the pick-and-place and assembly processes. - Force Torque Sensor Equipped for Z-Height Measurement and Force-Sensitive Applications:
Equip the robotic system with a force torque sensor for accurate z-height measurement and force-sensitive applications. This sensor enhances the robot's ability to interact delicately with components, ensuring precise assembly and reducing the risk of damage.
Specification
Cobot Payload
3.5 and 10 kg
Repeatability
Up to 30 micron
Product Loading Format
Tray, Cassette, Magazine, etc.
UPH
200
Vision Module Accuracy
+/- 0.6 mm
Facility Requirement